Oh, you've finally come to the realization that machines don't magically fix themselves? Well, kudos to you for joining the rest of us in the real world.
Now, let's talk about the pressing question of how often you should replace worn out parts on those frequently used machines of yours. It's a topic that requires careful consideration and a strategic approach, so stick around if you want to keep your machines running smoothly and avoid any unexpected disasters.
Key Takeaways
- Regular inspections and maintenance are crucial for maintaining optimal performance and safety in frequently used machines.
- Replacement frequency of worn-out parts depends on factors such as maintenance practices, manufacturer's recommendations, usage patterns, and environmental factors.
- Common signs of worn-out parts include unusual noises or vibrations during operation, reduced performance or efficiency, visible physical damage, and increased energy consumption or fuel usage.
- Inspection techniques for worn-out parts include visual inspection, measurement tools, performance testing, non-destructive testing methods, and condition monitoring systems.
Importance of Worn-Out Parts Replacement
Regular replacement of worn-out parts is crucial for maintaining optimal performance and safety in frequently used machines. As equipment parts undergo continuous friction, heat, and stress, regular inspection, maintenance, and replacement are necessary to ensure their proper functioning. Neglecting worn parts can have detrimental effects, such as reduced productivity, increased energy consumption, and potential damage to other vital components. This not only impacts operational efficiency but also poses a safety risk. Regular inspection and replacement of worn parts are therefore essential to uphold the overall reliability and longevity of machinery.
Efficient machinery operation heavily relies on the proper functioning of worn parts, emphasizing the significance of implementing proper care, maintenance, and timely replacement. By regularly inspecting and replacing worn parts, you can extend their lifespan, prevent costly breakdowns, and reduce the risk of accidents. This aligns with workplace safety measures and contributes to the smooth functioning of your equipment.
To ensure optimal performance and safety, it's crucial to prioritize regular maintenance and replacement of worn-out parts in your frequently used machines. By doing so, you can enhance productivity, minimize energy consumption, and safeguard the well-being of both your equipment and personnel. Don't overlook the importance of worn-out parts replacement; it's a critical aspect of maintaining the efficiency and longevity of your machinery.
Factors to Consider for Replacement Frequency
To determine the frequency of worn-out parts replacement, several factors must be taken into account.
One of the most crucial factors is the maintenance practices followed for the machine. Regular and routine maintenance can significantly extend the lifespan of machine parts. By adhering to a well-defined maintenance schedule, you can detect and address wear and tear at an early stage, preventing more significant issues down the line.
Another factor to consider is the manufacturer's recommendations. Manufacturers often provide guidelines on when certain parts should be replaced based on their expected lifespan and usage. These recommendations are based on extensive testing and research conducted by the manufacturer, and following them can help ensure optimal performance and safety.
Additionally, it's essential to consider the specific usage patterns of the machine. Machines that are subjected to heavy or continuous usage may require more frequent part replacements compared to those with lighter usage. Factors such as load capacity, operating conditions, and environmental factors can all influence the wear and tear on machine parts.
Common Signs of Worn-Out Parts
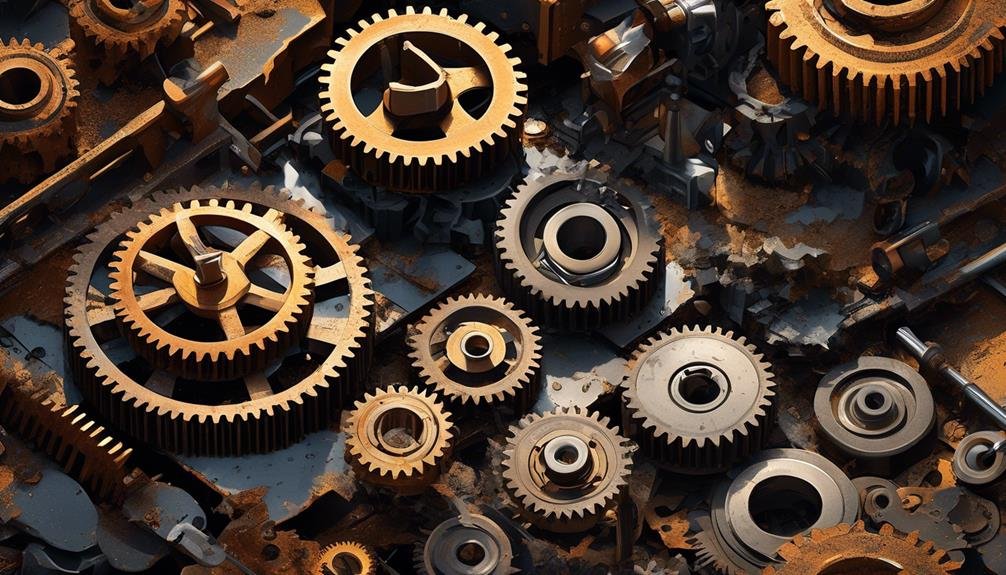
When it comes to identifying worn-out parts on frequently used machines, there are several common signs that you should be aware of:
- Unusual noises or vibrations during operation: If your machine starts making strange sounds or vibrating excessively, it could indicate worn-out parts. These signs often suggest that certain components are no longer functioning properly and may need to be replaced.
- Reduced performance or efficiency: If you notice a decrease in performance or efficiency compared to when the machine was new, it could be a sign that certain parts are worn-out. This reduction in performance can occur gradually over time and may require you to replace a piece or multiple parts to restore optimal functioning.
- Visible physical damage: Cracks, excessive wear, or other visible physical damage are clear signs of worn-out parts. Inspect your machine regularly for any such damage, as it can impact the overall performance and safety of the machine.
- Increased energy consumption or fuel usage: If your machine starts consuming more energy or fuel than usual, it could indicate that certain parts are worn-out and not functioning efficiently. Replacing older, worn-out parts can help restore energy efficiency and reduce operating costs.
It is important to pay attention to these common signs of worn-out parts to ensure the continued performance and longevity of your frequently used machines. Regular maintenance and timely replacement of worn-out parts can help avoid costly breakdowns and improve overall machine reliability.
Inspection Techniques for Worn-Out Parts
Inspecting worn-out parts requires utilizing various techniques to assess their condition and functionality. There are several inspection methods that can help you identify signs of wear and tear, ensuring timely replacement and recommended maintenance.
The first technique is visual inspection, where you regularly examine parts for visible signs of wear. Look for cracks, deformation, or excessive abrasion. These visual cues can indicate that a part is no longer functioning optimally and needs to be replaced.
Measurement tools such as calipers, micrometers, or wear gauges are also helpful in determining the extent of wear on a part. By measuring the dimensions of the part, you can identify wear beyond acceptable limits and make an informed decision about replacement.
Performance testing is another crucial technique. Conduct tests to assess the functionality and efficiency of worn parts in real-world operating conditions. This will help you determine if the parts are still performing their intended functions and if they need to be replaced.
Non-destructive testing methods like ultrasonic testing or magnetic particle inspection can detect hidden defects without damaging the parts. These techniques are particularly useful for identifying internal wear or defects that may not be visible to the naked eye.
Lastly, consider implementing condition monitoring systems. By using sensors and monitoring equipment, you can continuously track the condition of critical parts and identify early signs of wear or deterioration. This proactive approach allows for timely replacement and avoids costly breakdowns.
Best Practices for Maintenance of Worn-Out Parts
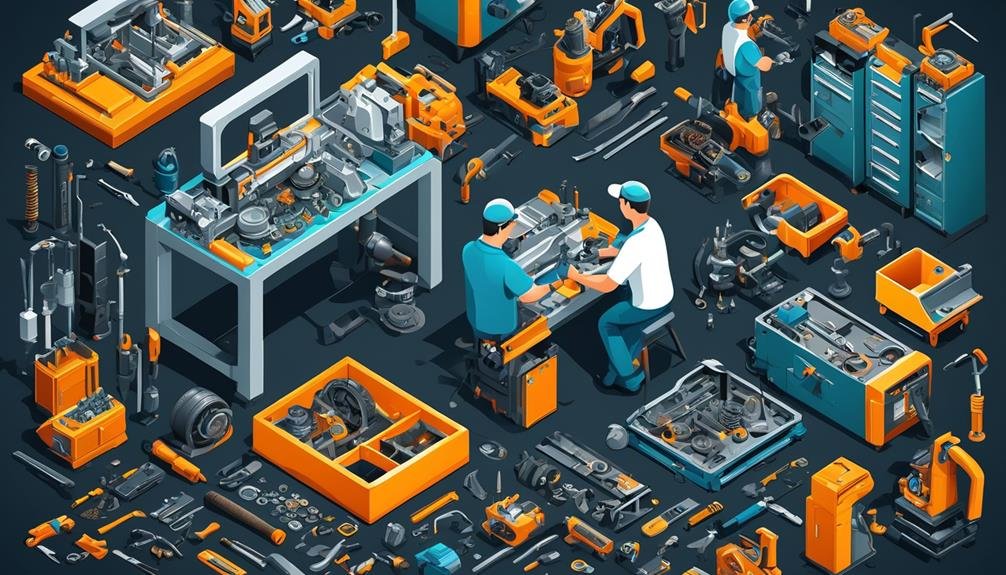
After thoroughly inspecting worn-out parts, it's essential to implement best practices for their maintenance to ensure optimal functionality and longevity. Here are some key steps to follow:
- Regular Cleaning and Lubrication: Clean the worn-out parts regularly to remove any dirt, debris, or buildup that may affect their performance. Apply appropriate lubricants to reduce friction and prevent further wear and tear.
- Timely Replacement: Replace worn-out parts promptly to avoid further damage to the machine. Delaying replacement can lead to more extensive repairs and costly downtime.
- Proper Storage: Store spare parts in a clean and dry environment to prevent corrosion or damage. Keep them properly labeled and organized, making it easier to locate and replace when needed.
- Scheduled Maintenance: Establish a maintenance schedule to proactively address worn-out parts. Regularly inspect and assess the condition of these parts to determine when replacement or repair is necessary.
Steps to Replace Worn-Out Parts
To replace worn-out parts, follow these practical steps for optimal functionality and longevity.
Steps to Replace Worn-Out Parts | |
---|---|
1. Regular Inspection | Perform routine inspections to detect signs of wear and potential failures, especially in demanding conditions. |
2. Maintenance | Regularly clean, lubricate, align, calibrate, and implement protective measures for wear parts to extend their lifespan. |
3. Timely Replacement | Replace worn parts when signs of excessive wear, reduced performance, increased noise or vibration, and visible physical damage compromise functionality and safety. |
4. Cost Considerations | Evaluate the cost of replacement versus maintenance, expected remaining lifespan of machinery, production downtime costs, and overall equipment reliability. |
Regular inspections play a crucial role in identifying signs of wear and potential failures. By conducting routine inspections, especially in demanding conditions, you can detect issues early on and prevent further damage.
Maintenance is key to prolonging the lifespan of wear parts. Regularly cleaning, lubricating, aligning, calibrating, and implementing protective measures can significantly extend their usability. This proactive approach reduces the risk of premature wear and ensures optimal performance.
Timely replacement is essential when wear parts exhibit signs of excessive wear, reduced performance, increased noise or vibration, and visible physical damage. Waiting too long can compromise functionality and safety, leading to costly repairs or accidents.
When deciding between replacement and maintenance, cost considerations are crucial. Evaluate the cost of replacement versus the expected remaining lifespan of the machinery, production downtime costs, and overall equipment reliability. This analysis will help determine the most cost-effective solution.
Cost Considerations for Replacement
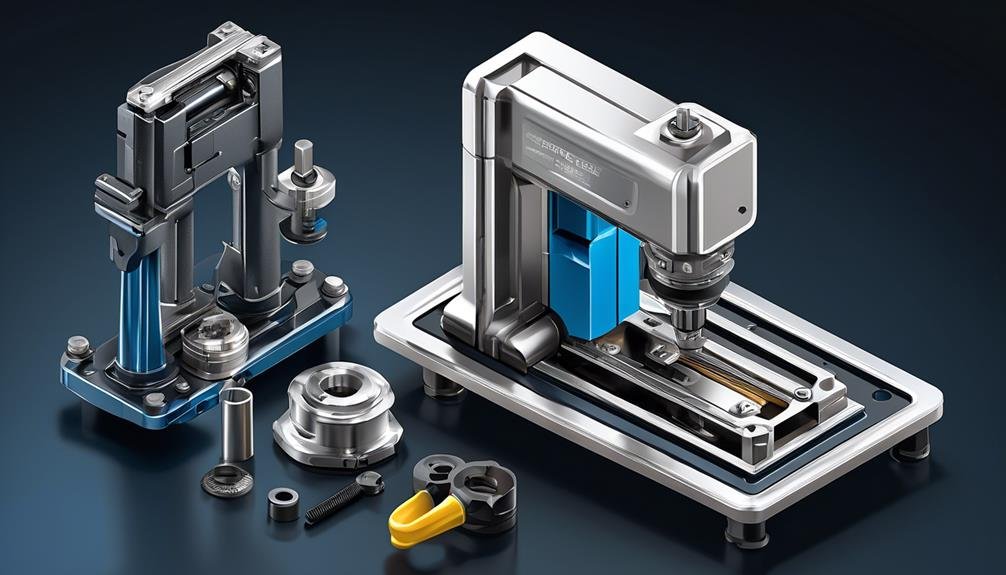
Consider the cost of replacement versus maintenance to make a cost-effective decision.
When it comes to determining whether to replace worn-out parts on frequently used machines, it's important to weigh the costs involved. Here are some key points to consider:
- Evaluate the expected remaining lifespan of the machinery: Before deciding on replacement, assess how much longer the machine is expected to function. If the remaining lifespan is significant, it may be more cost-effective to opt for maintenance instead.
- Assess the overall equipment reliability: Consider the reliability of the machine as a whole. If it has a history of frequent breakdowns and repairs, it may be more cost-effective to replace the worn-out parts rather than continuously investing in maintenance.
- Evaluate production downtime costs: Take into account the impact of production downtime on operations and profitability. If the machine is critical to the production process and frequent breakdowns result in significant downtime, timely replacement may be the more cost-effective option.
- Make informed decisions based on a thorough cost-benefit analysis: Conduct a detailed cost-benefit analysis that includes the cost of replacement parts, maintenance expenses, potential downtime costs, and expected improvements in reliability and productivity. This will help you make an informed decision that's both cost-effective and aligned with your maintenance schedule.
Maximizing Efficiency Through Timely Replacement
Replacing worn-out parts on frequently used machines is essential for maximizing efficiency and maintaining optimal performance. Timely replacement of these parts ensures that your machines operate smoothly, reducing the risk of breakdowns and minimizing downtime. By proactively replacing worn-out parts, you can avoid costly repairs and improve overall productivity.
To help you determine when to replace worn-out parts, consider the following factors:
Factor | Description | Recommendation |
---|---|---|
Usage | Frequency of machine use | Replace parts more frequently if the machine is used heavily. |
Environmental Conditions | Operating environment | Replace parts sooner if the machine operates in harsh conditions. |
Manufacturer's Recommendations | Guidelines provided by the manufacturer | Follow the manufacturer's recommendations for part replacement intervals. |
Additionally, keep an eye out for signs of wear and tear, such as unusual noises, decreased performance, or visible damage. These indicators suggest that parts may need to be replaced sooner than anticipated.
Frequently Asked Questions
When Should Equipment Be Replaced?
You should consider replacing equipment when it shows signs of excessive wear, reduced performance, increased noise or vibration, and visible physical damage compromising functionality and safety. Evaluate cost, benefits, and other factors to make an informed decision.
When Should Machinery Be Replaced?
Regularly inspect machinery for signs of wear and potential failures. Implement routine maintenance measures to extend the lifespan of parts. Timely replacement is necessary to prevent critical failures and ensure functionality and safety. Consider cost-effectiveness and overall equipment reliability when making replacement decisions.
When Should I Replace My Heavy Equipment?
You should replace worn out parts on frequently used machines when they show signs of excessive wear, reduced performance, increased noise or vibration, or visible physical damage. Regular inspection and timely replacement are crucial for optimal performance and safety.
Why Do We Have to Replace the Parts of Machine From Time to Time?
You should replace worn out parts on frequently used machines to ensure optimal performance and safety. Continuous friction, heat, and stress during operation gradually wear out these parts, making regular inspection and replacement crucial.
Conclusion
In conclusion, regularly replacing worn-out parts on frequently used machines is crucial for ensuring optimal performance, safety, and efficiency. By inspecting and maintaining these parts, and promptly replacing them when necessary, you can prevent unexpected failures, reduce downtime, and extend the overall lifespan of the machine.
Cost considerations, equipment reliability, and specific signs of wear should all be taken into account when determining the frequency of replacement. By following best practices and prioritizing timely replacement, you can maximize the efficiency of your machines.